High-voltage insulators are essential for electrical systems. They ensure safety and reliability in power transmission. To maintain these standards, rigorous testing and quality control processes are critical. This article explores various testing methods used in insulator production, including electrical testing and mechanical stress testing.
Importance of Testing and Quality Control
Testing is crucial in ensuring the reliability of high-voltage insulators. These components must withstand extreme conditions. They face high voltage, weather elements, and mechanical stresses. Quality control processes help identify defects before insulators are deployed. This reduces the risk of failures and enhances safety.
Electrical Testing Methods
Electrical testing evaluates an insulator’s ability to resist electrical stress. Several methods are used to assess electrical performance.
1. Dielectric Strength Testing:
This test measures the insulator’s ability to withstand high voltage without breaking down. A high voltage is applied to the insulator, and the point of failure is recorded. This test helps determine the maximum operating voltage for the insulator.
2. Power Factor Testing:
The power factor test assesses the insulation’s quality. It measures the ratio of real power to apparent power in an electrical circuit. A low power factor indicates better insulation performance. This test helps identify deterioration in insulator materials.
3. Insulation Resistance Testing:
Insulation resistance testing measures the resistance of the insulating material. A high resistance value indicates good insulation. This test helps detect moisture ingress and contamination that can affect performance.
4. Partial Discharge Testing:
Partial discharge testing identifies localized electrical discharges within the insulation. These discharges can indicate weaknesses in the insulator. Detecting partial discharge helps prevent future failures.
Mechanical Stress Testing Methods
Mechanical stress testing evaluates an insulator’s physical strength and durability. Various methods are employed to simulate real-world conditions.
1. Tensile Strength Testing:
This test measures the maximum amount of tensile (pulling) stress that an insulator can withstand before breaking. It helps determine the insulator’s ability to handle mechanical loads during installation and operation.
2. Flexural Strength Testing:
Flexural strength testing assesses how much bending stress an insulator can endure. Insulators often face bending forces due to wind or ice. This test helps ensure that the insulator can maintain its integrity under such conditions.
3. Impact Testing:
Impact testing simulates the effects of sudden force or impact on the insulator. It determines how well the insulator can resist damage from mechanical shocks. This test is crucial for ensuring reliability in harsh environments.
4. Aging Tests:
Aging tests simulate long-term exposure to environmental conditions. These tests include thermal cycling, UV exposure, and moisture immersion. By understanding how insulators degrade over time, manufacturers can enhance durability.
Quality Control Processes
Quality control processes ensure that insulators meet industry standards. These processes include inspections, testing, and documentation.
1. Incoming Material Inspection:
Before manufacturing, raw materials are inspected for quality. This ensures that only high-grade materials are used in production.
2. In-Process Inspections:
During the manufacturing process, in-process inspections are conducted. These inspections verify that production standards are being met. They help identify defects early, reducing waste and rework.
3. Final Inspection and Testing:
After production, insulators undergo final inspections and testing. All electrical and mechanical tests are conducted to ensure compliance with specifications. This step is crucial for ensuring product reliability.
4. Documentation and Certification:
Comprehensive documentation is maintained throughout the production process. This includes test results, inspection reports, and material certifications. Documentation is essential for traceability and quality assurance.
Conclusion
Testing and quality control are vital for the production of high-voltage insulators. Electrical and mechanical testing methods ensure that insulators can withstand demanding conditions. Rigorous quality control processes help identify defects and enhance reliability. By implementing these practices, manufacturers can produce safe and durable insulators that meet industry standards. The ongoing commitment to testing and quality assurance is essential for the future of high-voltage insulator technology.
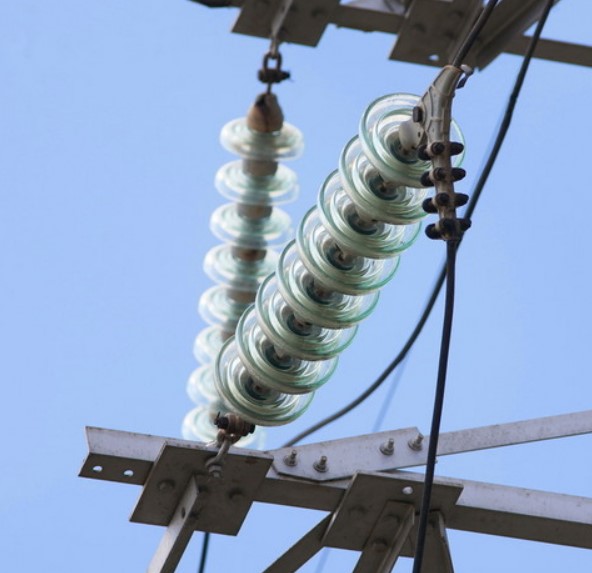