The performance and longevity of high-voltage insulators are critical for the reliability of power transmission systems. One key factor that affects an insulator’s durability and efficiency is its surface treatment. Different surface treatment techniques, such as coatings and sprays, are used to improve an insulator’s resistance to pollution and increase its durability. In this article, we will explore how these techniques are applied and their benefits.
The Importance of Surface Treatment
Insulators are exposed to various environmental conditions. These include dirt, pollution, moisture, and chemicals. Over time, these contaminants can accumulate on the surface of insulators, leading to leakage currents, flashovers, and even failure. Surface treatments act as protective barriers, helping to prevent contamination and prolonging the insulator’s lifespan.
Types of Surface Treatment
There are several surface treatment methods used in the production of insulators. Each method has its unique benefits, depending on the specific environment and application. Here, we discuss the most common ones.
1. Silicone Coating:
Silicone coatings are widely used in insulator manufacturing. They provide a hydrophobic (water-repellent) surface that prevents water and contaminants from forming conductive paths. Silicone coatings can “heal” after being damaged, as their hydrophobic properties migrate to the damaged area. This enhances the insulator’s resistance to pollution and moisture.
2. RTV (Room Temperature Vulcanizing) Coating:
RTV silicone coating is a popular choice for outdoor insulators. It is easy to apply and provides excellent protection against pollution. RTV coatings remain flexible and maintain their hydrophobic properties over time, even in harsh weather conditions. They also resist UV radiation and weathering, making them ideal for outdoor use.
3. Sprayed Zinc Coating:
Zinc coating, also known as metal spraying, is applied to the surface of ceramic and glass insulators. It offers corrosion protection by forming a barrier between the insulator and the environment. Zinc is particularly useful in coastal or industrial areas, where insulators are exposed to salt, sulfur, or other corrosive elements. Sprayed zinc coatings also improve the mechanical strength of insulators.
4. Polymer Coatings:
Polymer coatings are commonly used on composite insulators. These coatings are lightweight and offer good mechanical strength. They also provide a non-stick surface that prevents dirt and pollutants from accumulating. Polymer coatings are highly durable and resistant to UV radiation, moisture, and chemicals.
Enhancing Pollution Resistance
Pollution is a major challenge for insulators, particularly in urban and industrial areas. Contaminants like dust, salt, and chemicals can create conductive layers on the insulator’s surface. This can result in leakage currents, which reduce the insulator’s effectiveness and lead to failures.
Surface treatments, such as hydrophobic coatings, help combat pollution. By preventing water and pollutants from sticking to the surface, these treatments reduce the risk of flashovers. Hydrophobic coatings, like silicone and RTV, ensure that any water forms droplets and rolls off the surface instead of creating a continuous conductive film.
Improving Durability and Longevity
In addition to enhancing pollution resistance, surface treatments also improve the durability and longevity of insulators. Coatings protect the underlying materials from environmental wear and tear. For example, polymer coatings shield composite insulators from UV damage and corrosion, extending their service life.
Zinc spraying not only provides corrosion resistance but also strengthens ceramic and glass insulators against mechanical stress. This is especially important in areas with harsh environmental conditions, such as coastal regions or industrial zones.
Reducing Maintenance Costs
Effective surface treatments can reduce the need for frequent cleaning and maintenance of insulators. In polluted areas, insulators often require regular washing to remove contaminants and maintain performance. Coatings that repel pollutants and moisture reduce the accumulation of dirt, making it easier to maintain insulators over time. This leads to lower operational costs and fewer service interruptions.
Challenges in Surface Treatment Application
While surface treatments offer many benefits, there are challenges to their application. Some coatings, such as RTV silicone, may require reapplication over time due to wear. Additionally, the initial cost of applying coatings can be high. However, the long-term benefits, including improved performance and reduced maintenance, generally outweigh these costs.
Another challenge is ensuring uniform application. Poorly applied coatings can lead to uneven protection, leaving parts of the insulator exposed to environmental damage. Advanced techniques and equipment, such as robotic spray systems, are being developed to ensure consistent application.
Future Trends in Surface Treatment
As technology advances, new surface treatment methods are being developed to further improve insulator performance. Nanocoatings, for example, are emerging as a promising option. These coatings provide ultra-thin, high-performance barriers that enhance hydrophobicity and pollution resistance. Nanocoatings can also offer self-cleaning properties, further reducing the need for maintenance.
Additionally, research is being conducted on smart coatings that can detect surface damage or contamination. These coatings could alert maintenance teams to issues before they lead to failure, improving overall reliability.
Conclusion
Surface treatments play a vital role in improving the performance, durability, and pollution resistance of high-voltage insulators. Techniques such as silicone and RTV coatings, sprayed zinc, and polymer coatings help protect insulators from environmental damage, enhance their hydrophobic properties, and reduce maintenance costs. As new technologies like nanocoatings emerge, the future of insulator surface treatments looks promising, offering even greater protection and longevity for power transmission systems.
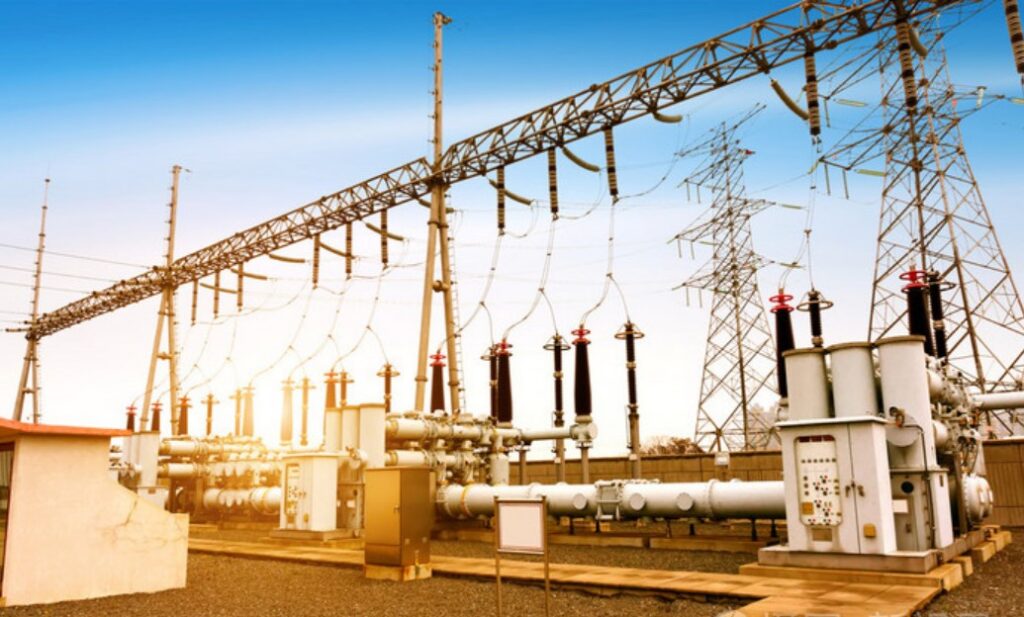