Composite insulators have become a preferred choice in high-voltage applications due to their superior performance compared to traditional ceramic and glass insulators. These insulators are lightweight, durable, and resistant to pollution, which makes them ideal for modern power transmission systems. The manufacturing of composite insulators involves several key processes, including molding and injection molding. This article explores these processes and highlights recent innovations in the production of composite insulators.
The Importance of Composite Insulators
Composite insulators are made from a combination of materials, typically including a fiberglass core, silicone rubber housing, and metal fittings. The fiberglass core provides mechanical strength, while the silicone rubber housing offers protection against environmental factors like moisture and pollution. Compared to ceramic and glass insulators, composite insulators have better performance in polluted environments, are lighter in weight, and are more resistant to mechanical impacts.
Compression Molding Process
One of the primary manufacturing techniques used for composite insulators is compression molding. In this process, the silicone rubber housing is formed around the fiberglass core under high pressure and temperature. The silicone rubber is placed into a mold, and the mold is compressed, forcing the rubber to take the shape of the mold. The pressure and heat cause the silicone to vulcanize, creating a solid and durable housing for the insulator.
Compression molding offers several advantages. It ensures uniform thickness of the silicone rubber, leading to better mechanical and electrical properties. Additionally, this process is cost-effective for producing large quantities of insulators, as it allows for high repeatability and consistent quality.
Injection Molding Process
Another common technique for producing composite insulators is injection molding. In this method, molten silicone rubber is injected into a mold cavity around the fiberglass core. The mold is then cooled, allowing the rubber to solidify and form the outer layer of the insulator.
Injection molding is highly efficient and can be automated, making it a popular choice for large-scale production. It offers more flexibility in terms of complex shapes and designs compared to compression molding. The process is also faster and results in minimal material waste, contributing to overall cost savings.
Material Innovations in Composite Insulators
Recent innovations in materials have further enhanced the performance of composite insulators. Advanced silicone compounds are now used to provide greater resistance to environmental degradation, such as ultraviolet (UV) radiation, extreme temperatures, and pollution. These new materials maintain their hydrophobic properties, which prevent water and dirt from adhering to the surface of the insulator, reducing the risk of flashovers.
Additionally, innovations in fiberglass materials have improved the mechanical strength and flexibility of composite insulators. New fiberglass compositions are more resistant to mechanical stress and fatigue, allowing insulators to withstand harsh environmental conditions, including heavy wind loads and ice.
Robotics and Automation in Manufacturing
The integration of robotics and automation into the manufacturing process has brought significant improvements in production efficiency and quality control. Robots are now used to handle the precise placement of the fiberglass core within the mold, as well as the injection and compression of silicone rubber. Automation ensures consistency, reduces human error, and increases the speed of production.
Automated systems also help in the application of surface treatments, such as hydrophobic coatings, which improve the insulator’s performance in polluted environments. By using robotics, manufacturers can achieve higher accuracy and repeatability in the production process, resulting in more reliable and durable insulators.
Quality Control and Testing
Quality control is a critical part of the manufacturing process for composite insulators. After production, each insulator undergoes rigorous testing to ensure it meets industry standards for mechanical and electrical performance. Tests include mechanical strength tests, where insulators are subjected to tensile forces, and electrical tests, which measure their ability to withstand high voltages.
Automated testing systems have improved the accuracy and efficiency of these processes. For example, computerized systems can perform continuous monitoring of production lines, identifying defects early in the process. This reduces waste and ensures that only high-quality insulators are shipped to customers.
Environmental Benefits of Composite Insulators
Composite insulators offer several environmental benefits compared to traditional ceramic or glass insulators. Their lightweight nature reduces the need for heavy structures, which minimizes material usage and transportation costs. Additionally, the durability of composite insulators leads to a longer service life, reducing the frequency of replacement and maintenance, which in turn lowers the environmental impact.
Innovations in recycling processes have also made it possible to repurpose materials from used composite insulators. This contributes to a more sustainable production cycle and reduces the waste generated by the power industry.
Future Trends in Composite Insulator Manufacturing
Looking ahead, several trends are expected to shape the future of composite insulator manufacturing. One trend is the development of smart manufacturing techniques that use data analytics and artificial intelligence (AI) to monitor and optimize production. This can lead to improved quality control, reduced waste, and lower production costs.
Another promising trend is the exploration of nanomaterials in composite insulator manufacturing. Nanomaterials can enhance the mechanical, electrical, and hydrophobic properties of insulators, making them even more resistant to environmental challenges. As research into nanotechnology progresses, we can expect to see more advanced composite insulators with longer service lives and enhanced performance.
Conclusion
The manufacturing processes of composite insulators, including compression molding and injection molding, play a vital role in producing high-quality, durable insulators for power transmission systems. Innovations in materials, automation, and testing have led to significant improvements in efficiency, performance, and sustainability. As technology continues to evolve, the future of composite insulator manufacturing looks bright, with further advancements expected in smart manufacturing and nanomaterials.
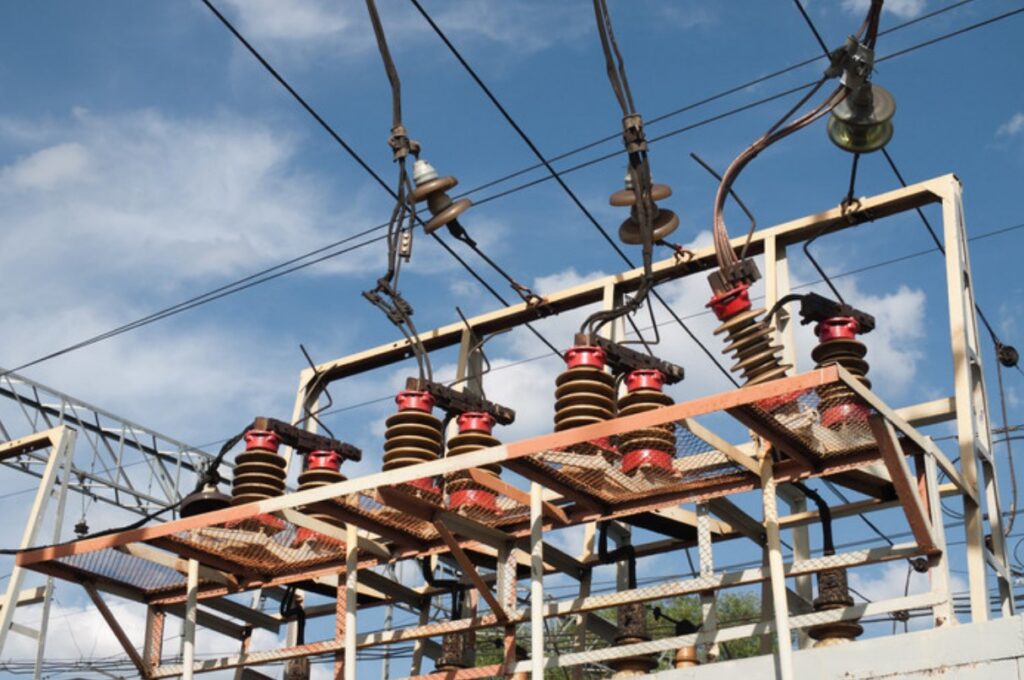