In the high-voltage transmission industry, choosing the right type of insulator is crucial for efficient and reliable power delivery. Ceramic and composite insulators are the two main types used worldwide, each with its own technical advantages and challenges. This article provides a comparison of ceramic and composite insulators, exploring their performance in various environmental and operational conditions.
Overview of Ceramic Insulators
Ceramic insulators, often made from porcelain, have been used in power systems for over a century. Known for their durability and high resistance to electrical stress, they are commonly used in harsh environments where extreme weather and pollution are concerns. The manufacturing process of ceramic insulators involves molding and firing materials at high temperatures, which creates a strong, dense structure that can withstand mechanical stress and resist aging over long periods.
One of the main advantages of ceramic insulators is their reliability. They are less susceptible to environmental degradation, making them a solid choice in polluted areas. However, they are heavy and require more structural support, which can increase installation costs and maintenance.
Overview of Composite Insulators
Composite insulators are made from a combination of fiberglass cores and silicone rubber housing, offering a lightweight and flexible alternative to ceramics. Their lower weight makes them easier to transport and install, reducing labor and logistical costs. Composite insulators also have high hydrophobicity, which prevents water and dust from sticking to the surface, helping maintain insulation performance under polluted conditions.
However, composite insulators have a shorter history of use, meaning long-term durability in various environments is still being studied. Additionally, some composites may be more prone to degradation from UV exposure, especially in regions with intense sunlight. Manufacturers are continuously working on improving materials to address these challenges.
Mechanical Strength and Flexibility
One of the key distinctions between ceramic and composite insulators lies in their mechanical properties. Ceramic insulators are rigid and have excellent mechanical strength, making them suitable for high-stress applications where stability is essential. This robustness is especially valuable in areas with high winds or heavy loads, where strong physical support is needed.
On the other hand, composite insulators offer more flexibility. Their fiberglass core provides mechanical strength, while the silicone rubber housing adds flexibility, allowing the insulator to better handle mechanical stress and vibrations. In regions with frequent seismic activity or areas requiring lighter support structures, composite insulators have a significant advantage.
Resistance to Environmental Degradation
Ceramic insulators have a natural resistance to environmental degradation due to their dense, impermeable structure. This makes them well-suited for coastal or industrial areas where pollution, salt, or chemicals can corrode materials. Their non-reactive surface is less affected by environmental factors, contributing to their longevity and low maintenance needs.
Composite insulators are also resistant to pollution but rely on the hydrophobic properties of their silicone rubber housing to repel contaminants. The hydrophobic surface prevents water and dirt from accumulating, which reduces the risk of flashover. However, UV exposure can gradually degrade the silicone, especially in sunny climates. Many manufacturers now incorporate UV-resistant materials to improve composite insulators’ durability.
Electrical Performance
In terms of electrical performance, both ceramic and composite insulators effectively prevent current leakage. Ceramic insulators have a high dielectric strength and are known for their stability under electrical stress, even at high voltages. However, during prolonged pollution exposure, contaminants on ceramic surfaces can lead to leakage currents, especially in humid conditions.
Composite insulators have a natural advantage in polluted environments due to their hydrophobic properties, which help maintain their insulating capabilities. The silicone housing on composite insulators allows contaminants to slide off more easily, reducing leakage currents and increasing reliability under high pollution.
Maintenance and Longevity
Ceramic insulators generally require less maintenance, making them a cost-effective choice for long-term installations. They are less prone to aging and are easy to clean, making them suitable for areas where regular maintenance is challenging. While their initial installation may be more costly due to weight, the reduced need for upkeep can offset these costs over time.
Composite insulators, while often requiring less initial investment, may need more frequent inspections and occasional surface treatments to maintain their hydrophobic properties. This is particularly important in environments with high UV exposure or significant pollution. Nevertheless, recent advancements in materials have improved the durability of composite insulators, making them a more competitive option for long-term use.
Cost Comparison
The initial cost of ceramic insulators can be higher due to their weight and the requirement for more robust support structures. However, this can be balanced out by their long lifespan and lower maintenance requirements. Ceramic insulators tend to be more cost-effective for installations where weight is not a limiting factor and where environmental conditions support long-term durability.
Composite insulators, on the other hand, often have lower installation costs due to their lightweight nature. In addition, they are less expensive to transport and install, especially in remote or challenging locations. The trade-off is the potential for higher maintenance costs over time, particularly in areas where environmental factors may impact the longevity of the silicone housing.
Future Trends in Insulator Technology
Composite insulator technology is advancing rapidly, with innovations in materials aimed at extending durability and UV resistance. Nanotechnology and advanced silicone compounds are being used to enhance hydrophobicity and improve resistance to environmental wear. These advancements make composite insulators increasingly viable for a wide range of applications, even in traditionally ceramic-dominated areas.
Conclusion
Both ceramic and composite insulators have distinct advantages and challenges, making them suitable for different applications and environments. Ceramic insulators offer excellent durability, mechanical strength, and reliability in polluted or coastal areas. Composite insulators, with their lightweight and flexible design, provide a viable alternative, particularly in remote or difficult-to-access locations where ease of installation is crucial. As technology advances, the choice between ceramic and composite insulators will continue to be influenced by innovations that enhance performance, longevity, and cost-efficiency in power transmission systems.
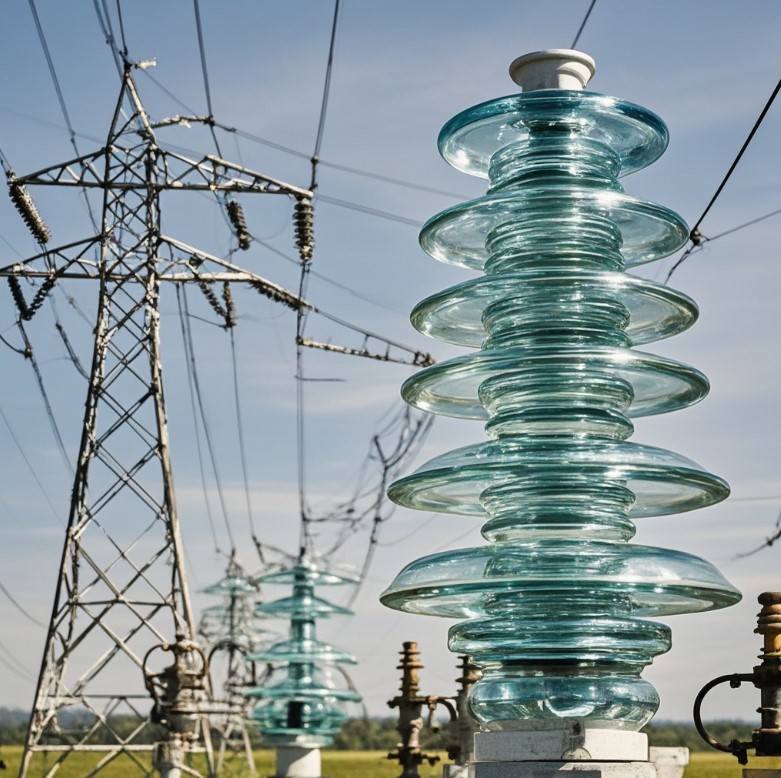